タップ加工の改善
加工技術
2020.06.11
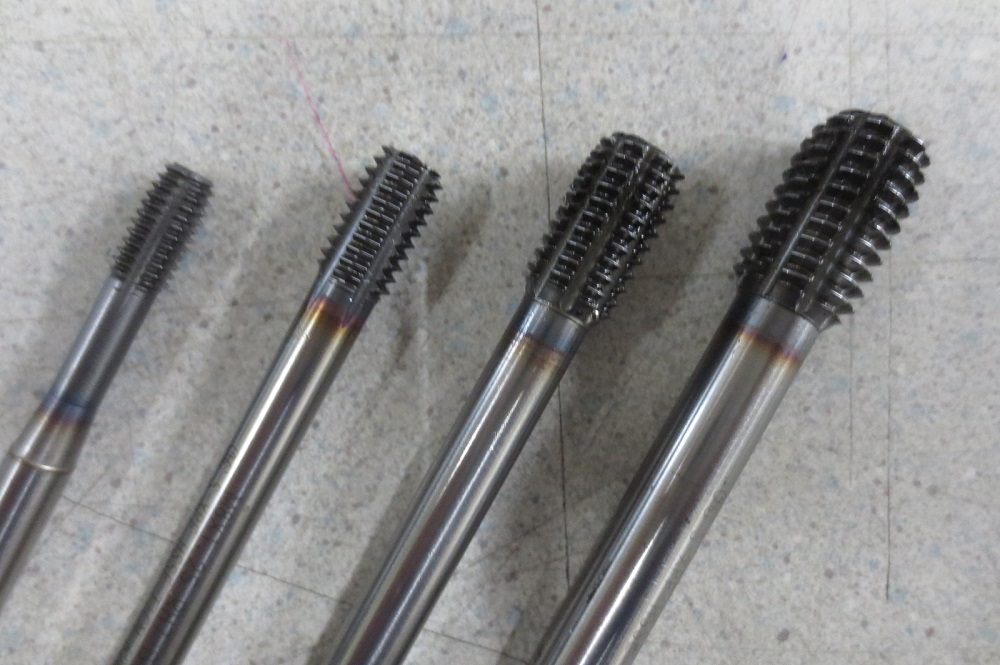
金型や金型部品製作でタップ加工(めねじ穴加工)は結構多い。
当社では、ドリルで下穴の加工して、口元を面取りした後でタップを使って機械加工でねじの加工を途中の深さまで行い、機械加工で行わなかった残りの深さまでをタップとタップハンドルを使い、手作業で加工している。
この手作業によるタッピングは人手も時間もかかるので、機械加工で穴の奥までタップ加工をしたいのですが、機械加工が故にタップの切れ味が悪くなっていることを感知できずタップを折ってしまうことがあり、折れたタップの除去には結構なコストがかかってしまうので、機械加工でのタップ加工は安全を見て浅めに加工している。
故に手作業の時間が削減できない。
タップが折れることが問題で、折れる要因を考えると
- タップの切れ刃部分が磨耗して切れ味が悪い
- タップの切れ刃部分に欠けがあり切れ味が悪い
- タップ加工で発生した切粉が穴の中で悪さをしている
- 下穴が曲がっている
- 下穴の穴径が小さい
などが考えられる。
下穴が曲がっていたり穴径が小さいものはタップ加工での問題ではなく、下穴のドリル加工に問題がある内容なのでここでは考えないものとする。
タップ折れの要因から「切れ味が良い」「切粉が出ない」タップを使えばよいので「転造タップ」が近いのではないかと考えられる。
転造タップとは、
下穴の円筒内面を削って溝を作るのではなく、塑性変形で盛り上がった山でねじを作る加工方法です。
従って切粉は排出されないので、削りカスでのトラブルは発生しませんし、下穴の奥までタップ加工をしても問題が発生することが極めて少ない。
タップの切れ味に対しては、切れ刃で削るタイプの工具ではないので、切削タップと比較して切れ味の低下するスピードが遅く長寿命である。
転造タップが折れにくい要因としてもう一つ、タップが芯径が太いことが考えられる。


転造タップを使用すれば、穴の奥までねじ加工ができて、手作業によるタッピングがほとんどなくなり、タップ折れの発生が減少し、タップも長寿命になる。
ここまでよいことばかり書いたが、注意しなければならないことが2点ある。
1つ目は、塑性変形でねじ山を作るので、下穴の径でねじ山の高さが決まってしまうので、タップの下穴径の管理が重要。
2つ目は、切削タップよりも加工に大きなトルク(回転力)を必要とし、大きな径には不向き。
当社では、M12以下のメートル並目ねじ加工に対しては転造タップを使用している。